摩擦可分两大类:滑动摩擦与滚动摩擦。本处将只着重讨论金属表面间的滑动摩擦。根据摩擦面间存在润滑剂的情况,滑动摩擦又分为干摩擦、边界摩擦(边界润滑)、流体摩擦(流体润滑)及混合摩擦(混合润滑),如以下动画所示。
边界摩擦、混合摩擦昧魈迥Σ炼急匦刖弑敢欢ǖ娜蠡条件,所以,相应的润滑状态也常分别称为边界润滑、混合润滑及流体润滑。可以用膜厚比λ来大致估计两滑动表面所处的摩擦(润滑)状态,即
式中: hmin--两滑动粗糙表面间的最小公称油膜厚度,μm ;
Ra1,Ra2--分别为两表面轮廓算术平均偏差,μm 。
当膜厚比λ≤l时,为边界摩擦(润滑)h态;当λ=l~5时,为混合摩擦(润滑)状态;当λ>5时,为流体摩擦(润滑)状态。
干摩擦是指表面间无任何润滑剂或保护膜的纯金属接触时的摩擦。在工程实际中,并不存在真正的干摩擦,因为任何零件的表面不仅会因氧化而形成氧化膜,而且多少也会被润滑油所湿润或受到"油污"。在机械设计中,通常都把这种未经人为润滑的摩擦状态当作“干”摩擦处理。固体表面之间的摩擦,虽然早就有人进行系统的研究,并在18世纪就提出了至今仍在沿用的、关于摩擦力的数学表达式:Ff=fFn(式中Ff为摩擦力、Fn为法向载荷、f为摩擦系数)。但是,有关摩擦的机理,直到20世纪中叶才比较清楚地揭示出来,并逐渐形成现今被广泛接受的分子--机械理论、粘附理论等。对于金属材料,特别是钢,目前较多采用修正后的粘附理论。
简单粘附理论于1945年由鲍登(F.P.Bowden)等人提出,他们认为两个金属表面在法向载荷作用下的接触面积,并非两个金属表面互相覆盖的公称接触面积(或叫表观接触面积)A0,而是由一些表面轮廓峰相接触所形 成的接触斑点的微面积的总和,叫真实接触面积Ar(下图)。由于真实接触面积很小,因此可以认为轮廓峰接触 区所受e压力很高。当接触区受到高压而产生塑性变形后, 这些微小接触面便发生粘附现象,形成冷焊结点。当接触 面相对滑动时,这些冷焊结点就被切开。在于摩擦条件下,可将较硬表面坚硬的轮廓峰在较软表面上犁出"犁沟"所需克服的阻力忽略不计,则摩擦力
式中:τB即是结点材料的剪切强度极限。
对于理想的弹塑性材料,当法向载荷增大时,真实接触面积Ar也随之增大,应力并不升高,而停留在材料的压缩屈服极限σsy。例如下图a所示为单个轮廓峰接触区在高压作用下产生塑性流动,导致接触面积增大到恰好能支承法向载荷为止的模型。故真实接触面积Ar为


单个轮廓峰接触模型
金属的摩擦系数为
式中τB、σsy是指相接触的两种金属中较软者的剪切强度极限与压缩屈服极限。由于大多数金属的τB/σsy 的比值均较接近,所以其摩擦系数相差甚小。但是,这个结论不完全符合实际。例如处于真空中的洁净金属发生摩擦时,其摩擦系数要比常规环境里的摩擦系数大得多。这一事实说明真实接触面积一定比简单粘附理论所指出的大得多。在简单粘附理论中,认为真实接触面积决定于软金属的压缩屈服极限和法向载荷。对于静态接触,这在大体上是正确的。为此,鲍登等人于1964年又提出了一种更切合实际的闭粘附理论。
这种理论认为,在摩擦情况下,轮廓峰接触区除作用有法向力外,还作用有切向力,所以接触区同时有压应力和切应力存在。这时金属材料的塑性变形取决于压应力和切应力所组成的复合应力作用,而不仅仅取决于金属材料的压缩屈服极限σsy。图<单个轮廓苯哟ツP>b所示为压应力σy及切应力τ联合作用下,单个轮廓峰的接触模型,并且假定材料的塑性变形产生于最大切应力达到某一极限值的情况。若将作用在轮廓峰接触区的切向力逐渐增大到Ff值,结点将进一步发生塑性流动,这种流动导致接触面积增大。也就是说,在复合绷ψ饔孟拢接触区出现了结点增长的现象。结点增长模型如图<单个轮廓峰接触模型>c所示,其中τB 为较软金属的剪切强度极限。
在真空中,洁净的金属表面发生摩擦时结点可能大幅度地增长,因此摩擦系数较高, 在空气中,由于界面上覆盖有一层氧化膜或污染膜,这种表面膜通常抗剪能力很弱,因而摩擦系数较低。修正后的粘附理论认为:
当两金属界面被表面膜分隔开时,τBj为表面膜的剪切强度极限;当剪断凵在较软金属基体内时,τBj为较软金属基体的剪切强度极限τB;若表面膜局部破裂并出现金属粘附结点时,τBj将介于较软金属的剪切强度极限和表面膜的剪切强度极限之间。
这个理论与实际情况比较接近,可以在相当大的范围内解释摩擦现象。在工程中,常用凼舨牧细钡哪Σ料凳是指在常规的压力与速度条件下,通过实验测定的,并可认为是一个常数,其值可参考有关资料。
边界摩擦(边界润滑)
当运动副的摩擦表面被吸附在表面的边界膜隔开,摩擦性质取决于边界膜和表面的吸附性能时的摩擦称为边界摩擦。润滑剂中的脂肪酸是一种极性化合物,它的极性分子能牢固地吸附在金属表面上。单分子膜吸附在金属表面上的符号如右上图a所示,图中o为极性原子团。这些单分子膜整齐地呈横向排列,很象一把刷子。边界摩擦类似两把刷子间的摩擦,其模型见右上图b。吸附在金属表面上的多层分子边界膜的摩擦模型如右下图所示。分子层距金属表面越远,吸附能力越弱,剪切强度越低,远到若干层后,就不再受约束。因此,摩擦系数将随着尾数的增加而下降,三层时要比一层时降低约一半。比较牢固地吸附在金属表面上的分子膜,称为边界膜。边界膜极薄,润滑油中的一个分子长度平均约0.002μm,如果边界膜有十层分子其厚度也仅为0.02μm 。金属表面粗糙的轮廓峰一般都超过边界膜的厚度(当膜厚比λ≤l时),所以边界摩擦时,不能完全避免金属的直接接触,这时仍有微小的摩擦力产生,其摩擦系数通常约在0.1左右。
按边界膜形成机理,边界膜分为吸附膜(物理吸附膜及化学吸附膜)和反应膜。吸附膜的吸附强度随温度升高而下降,达到一定温度后,吸附膜发生软化、失向和脱吸现象,从而使润滑作用降低,磨损率和摩擦系数都将迅速增加。
反应膜是当润滑剂中含有以原子形式存在的硫、氯、磷时,在较高的温度(通常在150℃ ~ 200℃)下,这些元素与金属起化学反应而生成硫、氯、磷的化合物(如硫化铁)在油与金属界面处形成的薄膜。这种反应膜具有低的剪切强度和高熔点,它比前两种吸附膜都更稳定。
合理选择摩擦副材料和润滑剂,降低表面粗糙度值,在润滑剂中加入铝康挠托蕴砑蛹梁图压添加剂,都能提高边界膜强度。
多层分子边界
膜的摩擦模型
混合摩擦(混合润滑)
当摩擦表面间处于边界摩擦与流体摩擦的混合状态时(膜厚比λ=l~5),称为混合摩擦。混合摩擦时,如流体润滑膜的厚度增大,表面轮廓峰直接接触的数量就要减小,润滑膜的承载比例也随之增加。所以在一定条件下,混合摩擦能有效地降低摩擦阻力,其摩擦系数要比边界摩擦时小得多。但因表面间仍有轮廓峰的直接接触,所以不可避免地仍有磨损存在。
流体摩擦(流体润滑)
当摩擦面间的润滑膜厚度大到足以将两个表面的轮廓峰完全隔开(即λ>5)时,即形成了完全的流体摩擦。这时润滑剂中的分子已大都不受金属表面吸附作用的支配而自由移动,摩擦是在流体内部的分子之间进行,所以摩擦系数极小(油润滑时约为0.001~0.008),而且不会有磨损产生,是理想的摩擦状态。
上课模式:倍杰电脑学校所有课程采用一对一教学,随到随学,学会为止的上课模式,以学员为根本,以就业为导向,毕业推荐就业!免除学员的后顾之忧!
倍杰课程有包含:CAD制图、办公软件、室内设计、平面设计、UG三维造型编程、solidworks三维设计、PLC编程、青少儿计算机编程等。
张家港倍杰电脑培训学校专业专注电脑软件课程培训15年!
地址:张家港长安南路49号西城大厦4楼(市区医院往北20米)
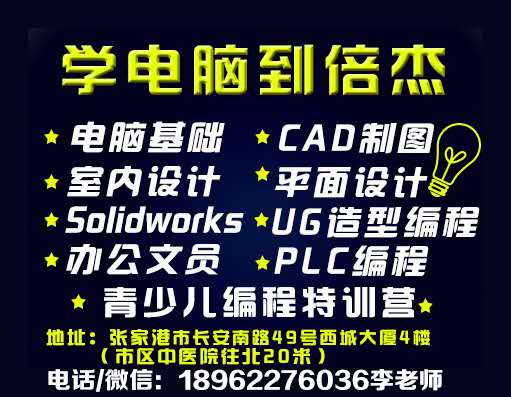
